RF96
RF96 è il progetto di tesi triennale di Federico, il quale ha messo in questo progetto tutte le conoscenze acquisite nella triennale, l'esperienza nel settore aeronautico e la tecnologia della stampa 3D, riuscendo a realizzare un prototipo in scala radiocomandato perfettamente funzionante, lo scopo della tesi era quello di dimostrare come la stampa additiva potesse essere una soluzione alla realizzazione di prototipi funzionanti in una fase di ricerca e sviluppo al fine di ottenere feedback reali con costi contenuti.
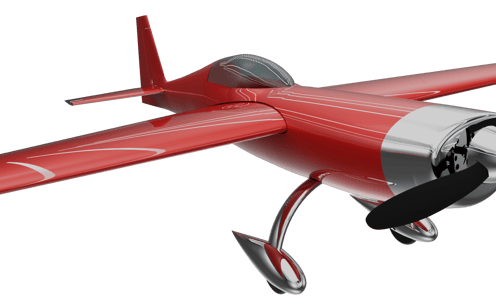
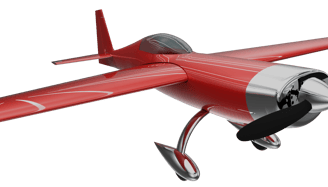
PROGETTAZIONE
Sin dal principio si è cercato di realizzare le geometrie tramite CAD con un attento occhio ad ottimizzarle per la stampa 3D, sono stati presi in considerazione gli spessori, le centine interne all'ala sono inclinate di 45 gradi per autosostenersi e i vari pezzi sono stati suddivisi per poter essere stampati nella maggior parte delle stampanti.
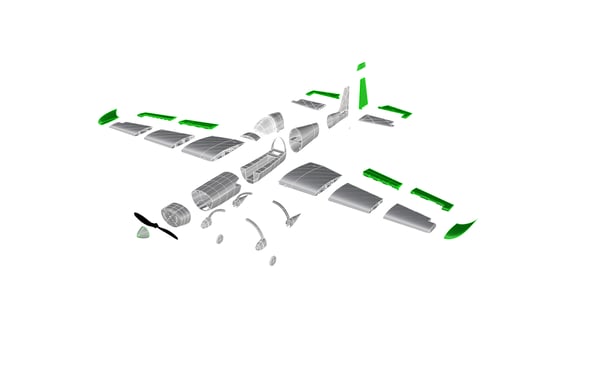
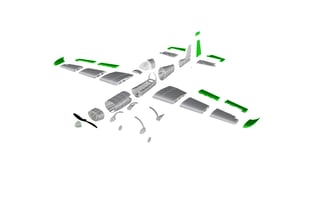
Fase 1:
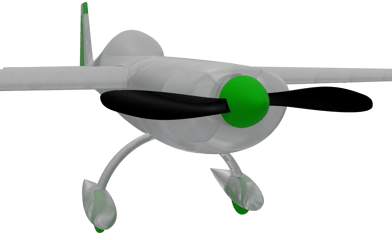
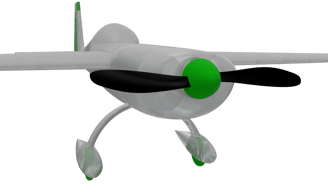
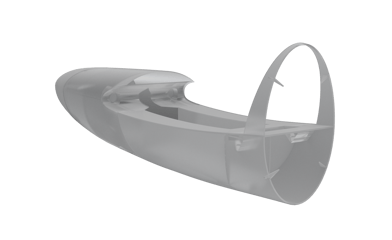
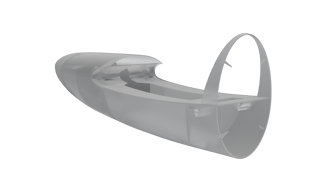
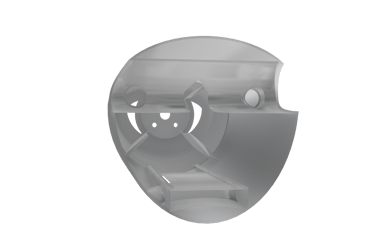
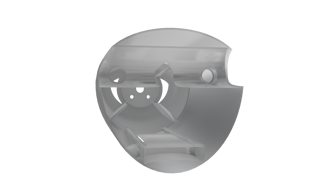
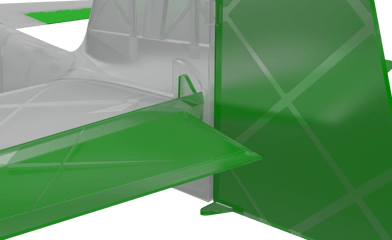
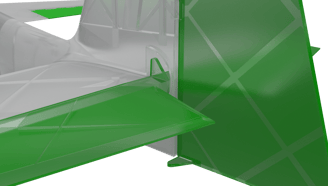
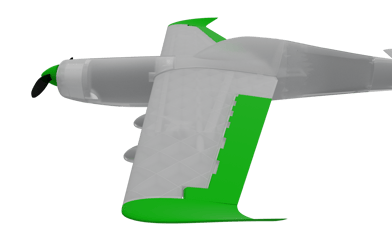
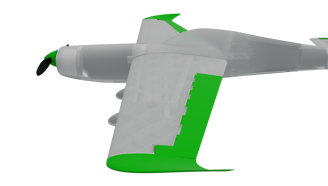
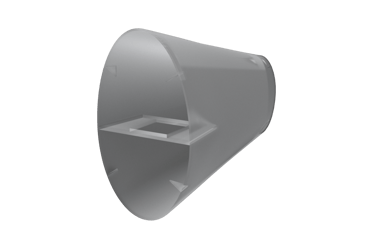
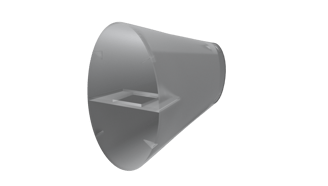
La fusoliera è stata divisa in 3 parti principali, la naca motore, con già previsti tutti gli attacchi per un motore Brushless elettrico preventivamente selezionato, la parte centrale con l'alloggiamento della batteria ed il fissaggio dell'ala ed infine il troncone di coda con l'alloggiamento dei servocomandi e la connessione alla deriva ed allo stabilizzatore orizzontale, tutti questi componenti sono stati pensati e modellati pensando già a come sarebbero stati stampati andando ad ottimizzare il peso, la resistenza strutturale ed agevolando la connessione delle parti
STAMPA 3D
Una volta ultimato il 3D, tutti i pezzi sono stati preparati per la stampa 3D, come materiale si è scelto il Pet-G, che ha ottime caratteristiche meccaniche e facilità di stampa, ad eccezione delle ruote stampate in TPU, un polimetro elastico che si è dimostrato perfetto per la realizzazione dei pneumatici
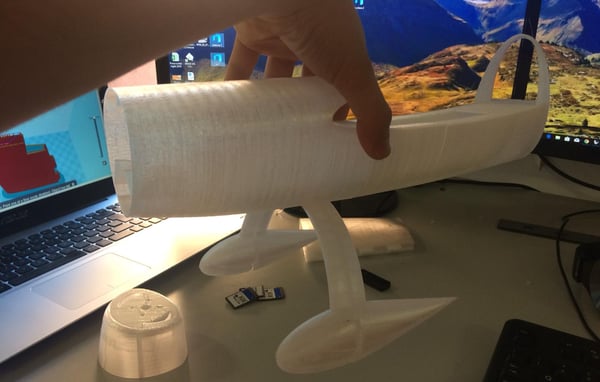
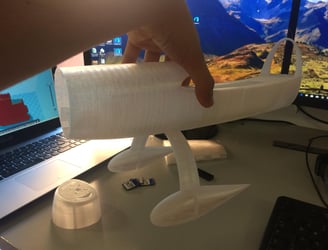
Fase 2:
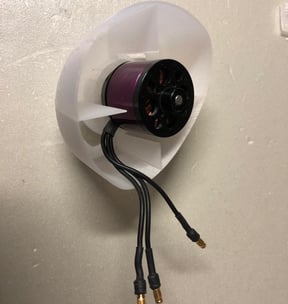
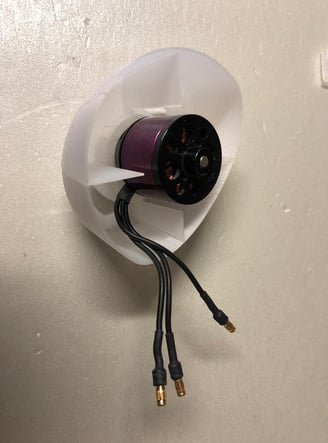
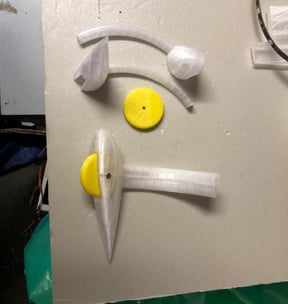
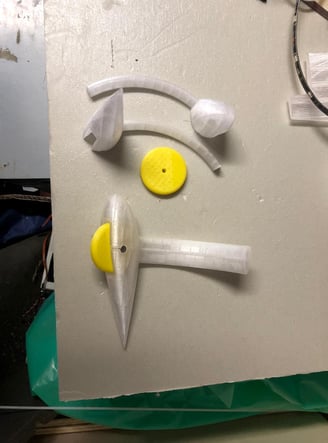

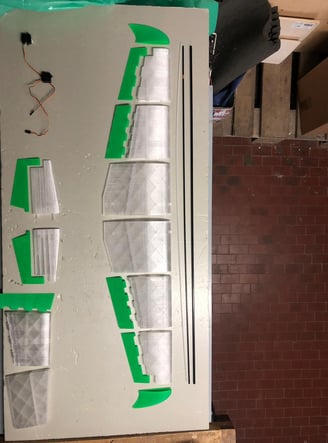
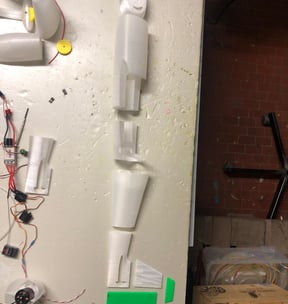
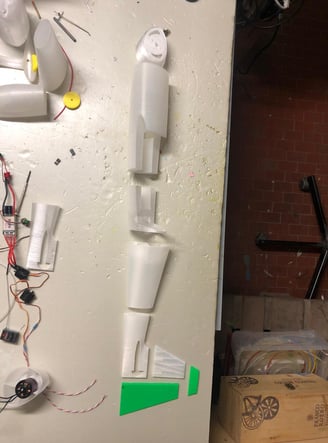
I componenti sono stampati sono stati verificati sia dal punto di vista strutturale che estetico e funzionale, sono stati verificati tutti gli accorgimenti, in alcuni casi è stato necessario riprogettare alcuni dettagli al fine di ottenere il risultato migliore
ASSEMBLAGGIO
Sin dal principio si è cercato di realizzare le geometrie tramite CAD con un attento occhio ad ottimizzarle per la stampa 3D, sono stati presi in considerazione gli spessori, le centine interne all'ala sono inclinate di 45 gradi per autosostenersi e i vari pezzi sono stati suddivisi per poter essere stampati nella maggior parte delle stampanti.
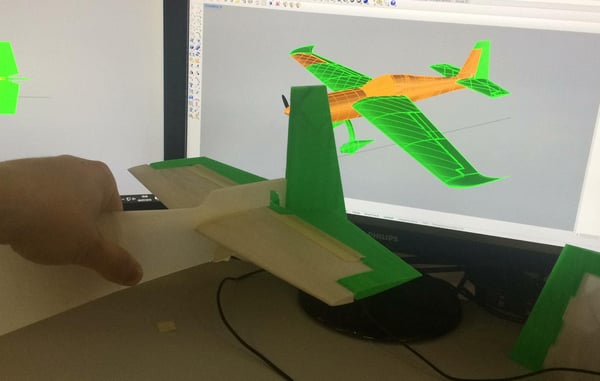
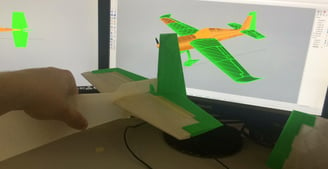
Fase 3:
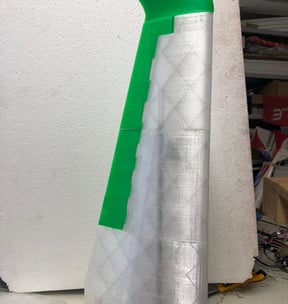
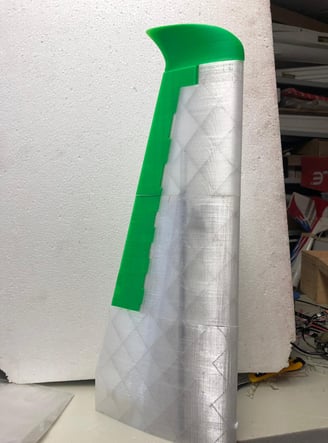
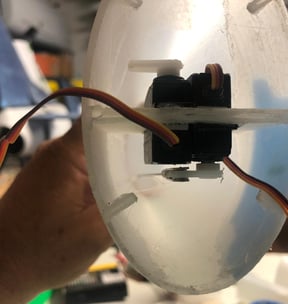
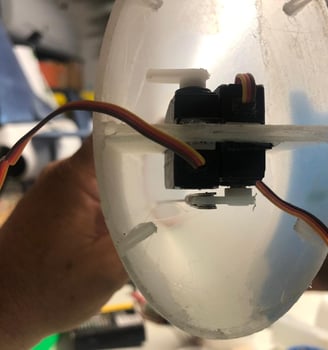
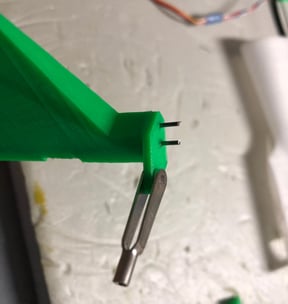
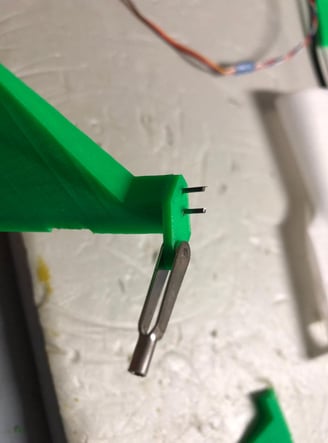
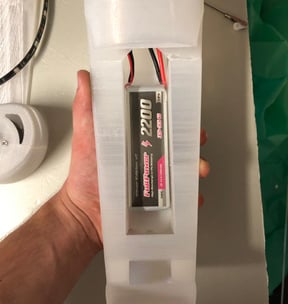
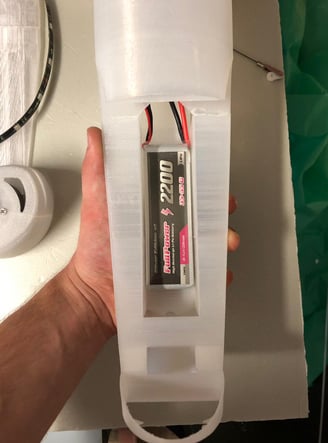
I componenti sono stampati sono stati verificati sia dal punto di vista strutturale che estetico e funzionale, sono stati verificati tutti gli accorgimenti, in alcuni casi è stato necessario riprogettare alcuni dettagli al fine di ottenere il risultato migliore
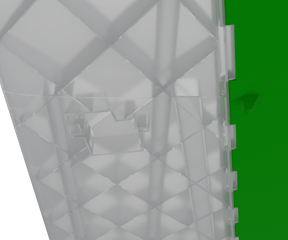
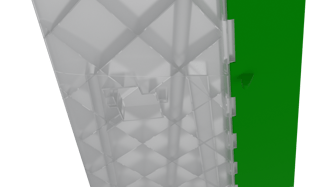
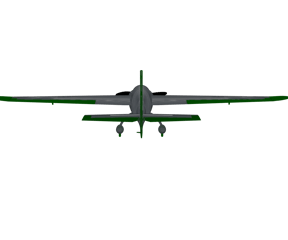
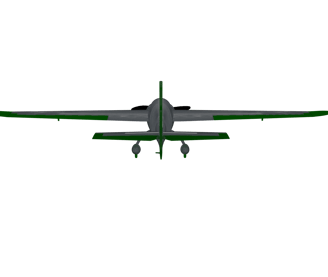
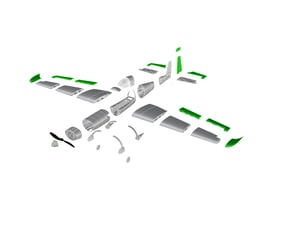
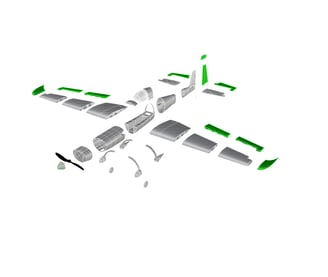
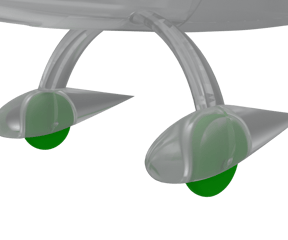
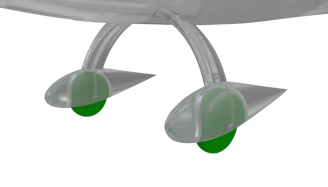
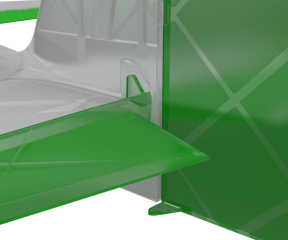
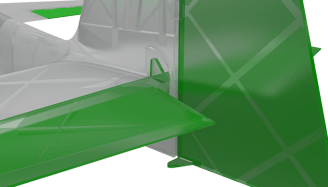
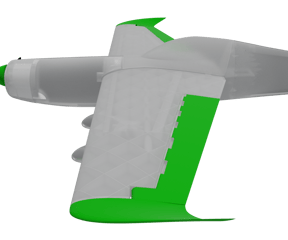
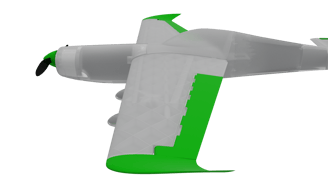
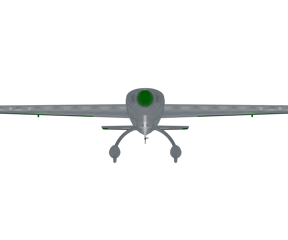
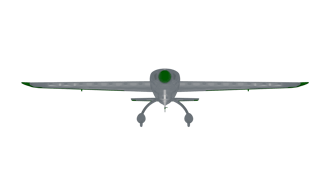
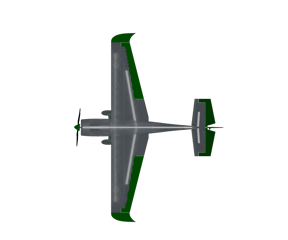
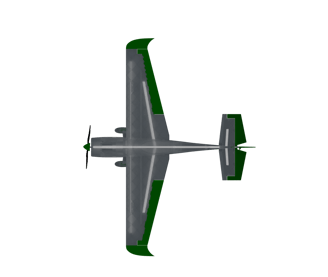
RENDER
Sono stati realizzati dei render per la presentazione durante l'esposizione della tesi, i render servono ad aiutare lo spettatore ad immaginarsi il prodotto finito, in questo caso il prototipo sarebbe stato più che sufficiente.
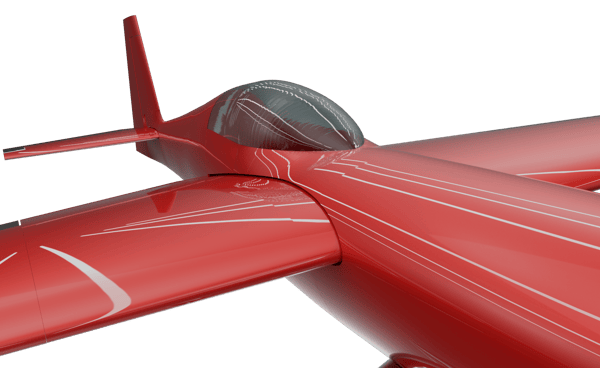
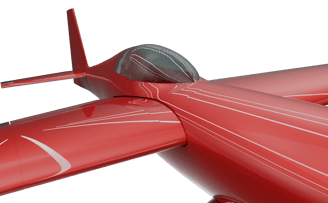
Fase 4: